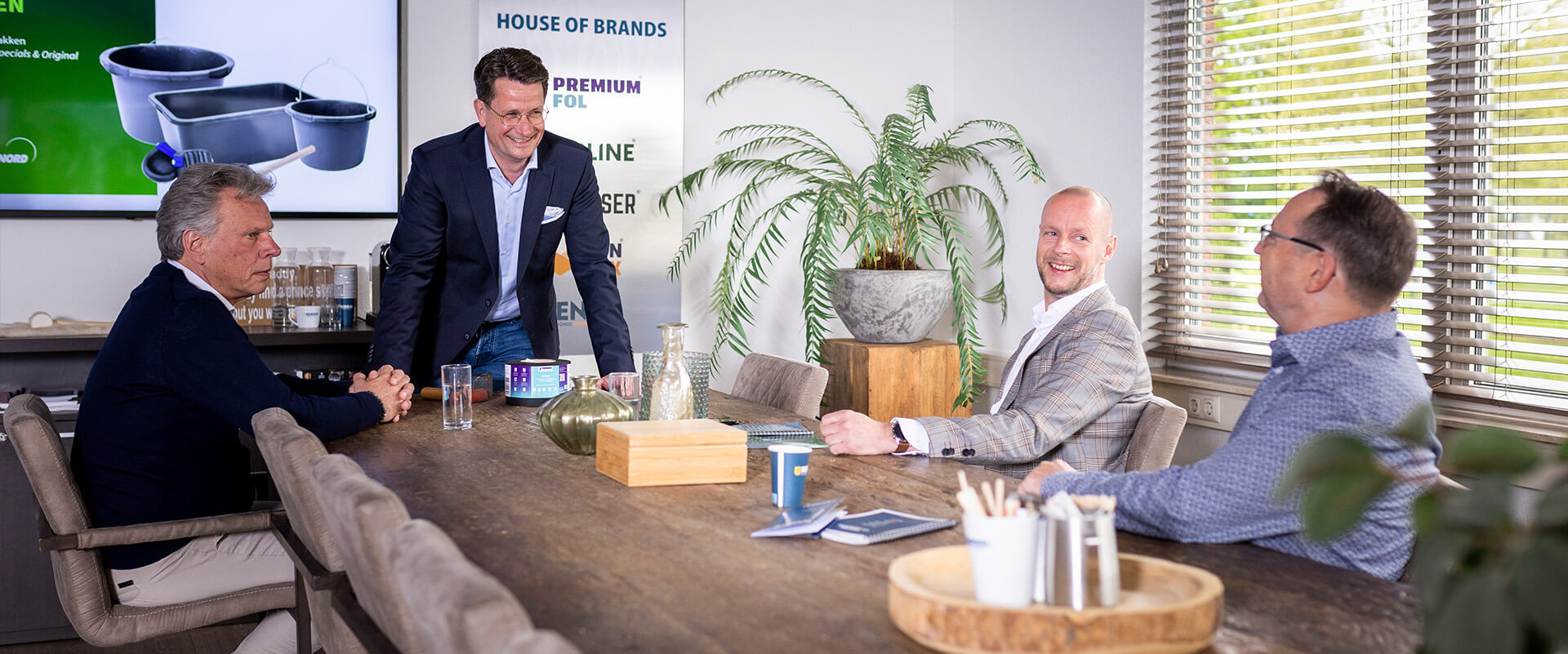
Grondstoffen
We streven naar een hoogwaardig assortiment rubber- en kunststofproducten en concepten dat volledig bestaat uit hernieuwbare grondstoffen. Zo behalen we gezamenlijke successen met zo min mogelijk belasting voor het milieu.
Berdal werkt al sinds de jaren negentig van de vorige eeuw aan een duurzamere bedrijfsvoering. Wij geloven dat thema’s als duurzaamheid en circulair bouwen vragen om innovatie en meer samenwerking in de gehele keten. Aan de hand van de speerpunten duurzaam ondernemen, klimaat, logistiek, mens en grondstoffen laten we zien welke concrete acties wij ondernemen wanneer het gaat om maatschappelijk verantwoord ondernemen.
We streven naar een hoogwaardig assortiment rubber- en kunststofproducten en concepten dat volledig bestaat uit hernieuwbare grondstoffen. Zo behalen we gezamenlijke successen met zo min mogelijk belasting voor het milieu.
Berdal stimuleert duurzamere keuzes. Bijvoorbeeld op het gebied van duurzaam omgaan met grondstoffen en energie en het verminderen van verpakkingsmateriaal.
Berdal denkt mee met haar partners over efficiënte logistiek. Om zo de druk op het wegennetwerk en het milieu te verminderen.
Het welzijn van mensen staat bij Berdal centraal. Dit komt tot uiting in het stimuleren van een goede werk-privébalans en gezonde gewoontes.
Wij geloven in duurzaamheid én transparantie. De duurzaamheid van onze producten wordt gewaarborgd door onafhankelijke keurmerken zoals Der Blaue Engel, Cradle to Cradle, GSES en EcoVadis.